Commonly used inspection methods in SMT patch processing
In SMT patch processing, welding quality inspection is crucial, and the quality of patch welding is directly related to the quality of the entire electronic processing product.
Commonly used inspection methods in SMT patch processing
1. Visual inspection: Visual inspection is one of the most common quality inspection methods, which can be used to check the correct placement of components, polarity, solder paste quality and solder joint appearance. Operators use microscopes or automatic visual inspection systems to inspect components and welding on PCBs.
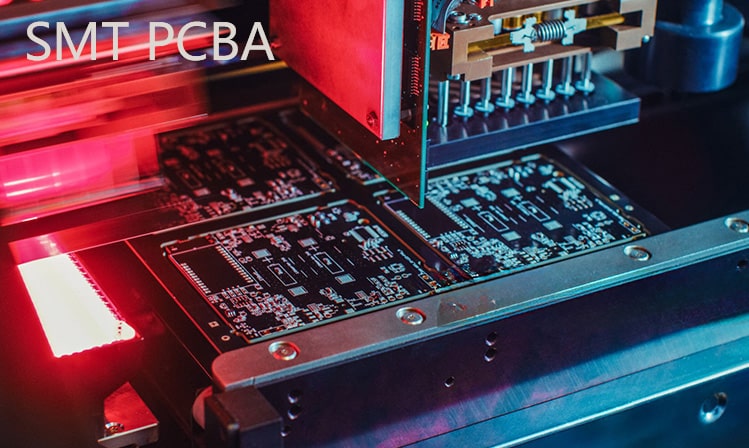
2. X-ray inspection: X-ray inspection can detect invisible internal defects, especially suitable for solder joint inspection of packaging forms such as BGA (ball grid array), which can provide accurate internal structure images and find problems that are difficult to find with traditional optical methods. This is especially important for the inspection of BGA (Ball Grid Array) components because their solder joints are usually located at the bottom of the component.
3. AOI (Automated Optical Inspection): Automated optical inspection systems use cameras and image processing software to check component placement and solder joint quality. Using optical imaging equipment and computer image processing technology, the position of components, quality of solder joints, defects, etc. on the PCB board can be automatically detected. It can detect subtle defects such as poor solder joints, offsets, missing parts, etc. It will not cause physical damage to the PCB board, and its detection speed is fast, suitable for mass production.
4. SPI (Solder Paste Inspection): Solder paste inspection is used to check the uniformity and correctness of solder paste to ensure that it is correctly applied to the PCB. This helps prevent subsequent soldering problems caused by solder paste problems.
5. ICT (In-Circuit Testing): In-circuit testing is a method used to detect the connectivity of electronic components and circuits. This includes checking component values such as resistance, capacitance and inductance, as well as detecting short circuits and open circuits.
6. Flying Probe Test: Using a movable test needle, contact the test points on the PCB board one by one to perform electrical performance testing. It is suitable for low-volume and prototype production and does not require a dedicated test fixture.
7. Functional Testing: Functional testing is used to verify the performance of the entire electronic product. It simulates the actual working environment of the product, tests the function of the entire PCB board, and ensures its normal operation in real applications, including checking various functions, communications, and interfaces. It can verify the performance of the circuit board in the actual use environment. Comprehensively test all functions to ensure the final performance of the product.
8. Environmental Testing: Environmental testing includes temperature cycling, humidity testing, vibration and impact testing, etc. to evaluate the reliability and durability of electronic products under various environmental conditions.
These testing methods are usually used in combination to ensure the quality and reliability of electronic processing products. The selection of appropriate testing methods depends on production requirements, electronic product types, and quality standards.
If you want to know more, you can pay attention to PCBAMake. If you need to know more about PCB proofing, SMT patch, and PCBA processing related technical knowledge, please feel free to contact us!